While it is well known that Rolls Royce licensed Citroën hydraulic suspension for their Silver Shadow and Silver Spirit models, another Brit, Colin Chapman, founder of Britain’s Lotus Cars Ltd., developed the original concept of computer management of hydraulic suspension in the 1980s to improve cornering in F1 racing cars.
Citroën’s first use of hydraulic (aka — hydropneumatic) suspension appeared in 1954. Developed by Paul Magès at Citroën, it was installed to the rear end of the Traction Avant 15-6 (designated as a 15-6H), before becoming the means for complete suspension of the new DS model introduced in 1955.
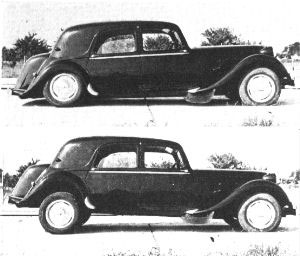
The hydraulic pressure was supplied by a high pressure hydraulic pump driven from the engine. The pump pressurized an accumulator sphere from where regulated fluid pressure was fed to a sphere at each wheel. Each sphere was charged with Nitrogen and contained a flexible membrane that separated the nitrogen gas from the varying fluid. As the nitrogen was compressed, offering six times the compressibility of the steel springs used by vehicles up to this time, the result was Citroën’s famous DS floaty ride.
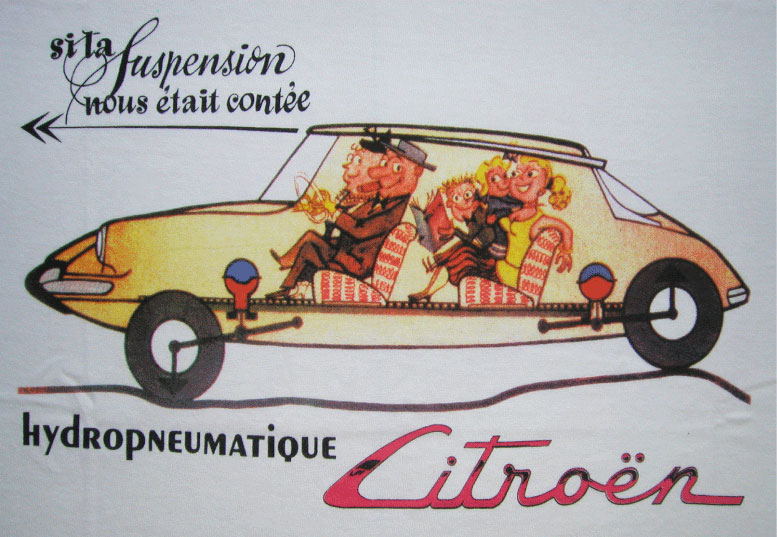
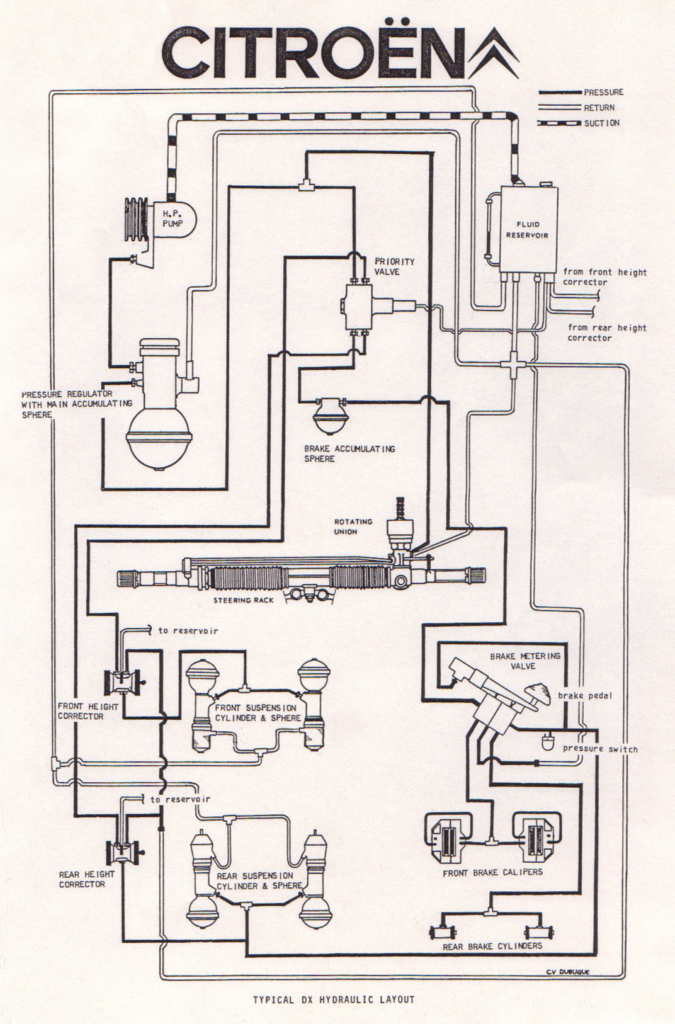
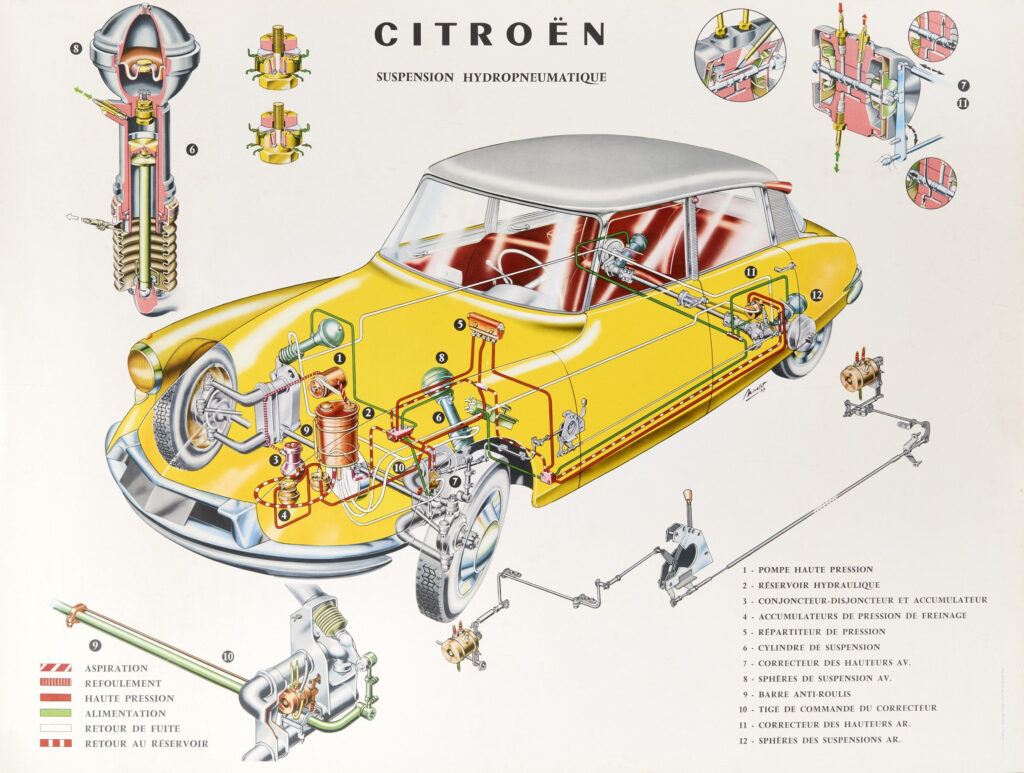
In 1983, Lotus raced an active (non-hydraulic) suspension car [Type 92-Cosworth], that had an onboard computer that wasn’t just recording data but actually having an effect on its dynamics.
As well as sensing bumps in the road, the Lotus active suspension system read the forces acting on the car body. The computer could respond to these forces, which would normally cause body roll, dive under braking, and similar motions.
Succeeding with their F1 effort, Lotus fitted and developed a prototype system to a 1985 Excel with electro-hydraulic active suspension, but never offered it for sale to the public. Instead, Lotus tried to get some benefits from this technology they developed for the F1, offering it for consideration by building demonstration cars for Volvo, General Motors, and other car makers.
It was reported in the July 1986 issue of Popular Science Magazine that Volvo was testing it in a modified 740 model using the Lotus suspension system.
“Under the hood, hydraulic struts were fitted in place of the stock MacPherson struts. The struts are controlled by a central computer that is wired to sensors that measure movement at each wheel and the roll, pitch, and yaw of the body. Coined Computer Controlled Suspension by Volvo, the system avoids many of the trade-offs inherent in springs and shocks. The hydraulics react within 5^.000 second, and can cycle up to 1,500 times a minute. The large tank stores oil for the hydraulic system. On Volvo’s prototype, engineers can reprogram the suspension with a lap-top computer, changing ride and handling characteristics.“
Sensors continually monitor body movement and vehicle ride level, constantly supplying the computer with new data. As the computer receives and processes data, it operates the hydraulic servos, mounted beside each wheel. Almost instantly, the servo-regulated suspension generates counter forces to body lean, dive, and squat during driving maneuvers.
It was similar to the system that Citroën developed for the XM, and refined further as “Activa” to put on Xantia.
The distinguishing feature of Activa was the ability to drive around curves without any body roll.. It was an extension to the XM’s Hydractive II suspension, where two additional spheres and two hydraulic cylinders are used together with computer control acting on the cross-stabilizer bars to eliminate body roll completely.
The Citroën Xantia V6 Activa performed impressively with a record speed of 85 km/h (53 mph) through the moose test maneuver, (conducted by the magazine Teknikens Värld’s, as a test of avoiding a moose in the road.) In reality, the test is constructed to simulate, for example, a reversing car or a child rushing out onto the road.This is because it is more likely that the moose will continue across the road than remain in place or turn back, making it more advisable to brake hard and try to slip behind the animal than to swerve in front of it.
The moose test is performed on a dry road surface. Traffic cones are set up in an S shape to simulate the obstacle, road, and road edges. The car to be tested has one belted person in each available seat and weights in the boot to achieve maximum load. In order to qualify as a “pass” the vehicle must successfully navigate the course at 72 km/h (45 mph). When the driver comes onto the track, they quickly swerve into the oncoming lane to avoid the object and then immediately swerve back to avoid oncoming traffic. The test is repeated at an increased speeds until the car skids, knocks down cones, or spins around.
Along with active suspension Volvo was testing many things in the 80s. One of them was an energy saving inertia flywheel. The energy normally wasted when braking was stored in a wind-up flywheel similar to a modern brake regeneration system. Alas it was deemed, too complicated, too expensive and therefore was never implemented on production vehicles.
What about the Mercedes 450 SEL 6.9? Didn‘t it use the Citroën Hydropneumatic? Also the early Porsche 911 Models had it optionally on the front axle, as far as I know.
Mercedes-Benz developed their own hydropneumatic system for the 450 SEL 6.9. It differred in that it used the timing chain to drive the hydraulic pump instead of the rubber belt in Citroën’s system. While the Citroën system used a single pump for braking, power steering, power clutch (when equipped with semi-automatic transmission), and suspension, Mercedes used separate pumps for brake boost, power steering, and suspension, citing the better fail-safe measures than Citroën in the event of a hydraulic failure. Both manufacturers had different approaches when the cars were parked and switched off. Citroën cars lowered themselves closer to the ground while Mercedes did not. Also the Mercedes-Benz suspension system has the feature that maintains body level without squatting at the rear or diving in the front during the acceleration and braking respectively.
I don’t know about the Porsche 911. Active Suspension Management (dynamically adjustable dampers) was available on the 997 in 2005.
Mercedes developed its own hydraulic system based on the Citroën model. Period.
A hydraulic pump driven by a timing chain is simply stupid, as there is a separate pump for each function. This drives up maintenance costs immeasurably (at least you have a sight on the hood), but offers no better safety precautions in the event of a hydraulic failure. If part of the separate Mercedes system fails, you’re left on the side of the road, just like with Citroën.
Furthermore, Citroën has not only developed a hydropneumatic suspension, but also a Hydractive suspension and has further advanced it with an anti-sink system (brake support ball) on Hydractive II and an electronic pump on Hydractive III and IV.
I don’t know if Citroën was unwilling to license a hydraulic suspension, or if all the other carmakers in the world were foolish enough to believe that springs with shock absorbers were comparable to such an advanced ( though expensive) suspension system.
I believe that if a German car manufacturer had developed such a hydractive system instead of Citroën (who cares about that French car), we would have at least 75% of our cars with hydractive suspension today.
Porsche offered the Boge Nivomat system on the original 911E in 1969 and as an option on the 911S and T. This system was entirely contained in the shock absorber:
https://www.drive2.ru/l/484993755452015312/
It contained a regular shock and a pressurized gas chamber. The system would raise or lower pressure in the gas chamber just like a Citroën, but did not have an external pump. It merely used pressure built in the shock through the car’s motion to increase pressure and level the car.
It was not offered by Porsche very long – the 911s so fitted had a totally different front suspension without torsion bars. But Boge offered it for a long time as an aftermarket item, mainly for German and Swedish cars.